Services offered at the Laboratory include:
- Product testing and evaluation using either the product(s) directly or test specimens taken from the product(s) by die or machine cutting.
- Material testing and evaluation of raw materials or test specimens prepared by injection and compression moulding then die cutting or milling.
- Identification and analysis of polymeric materials using Differential Scanning Calorimetry (DSC) along with Infrared Spectroscopy.
- Flow behaviour of materials such as melt flow rate and shear rate verses viscosity of materials can be determined using the Melt Flow Indexer
Laboratory Services
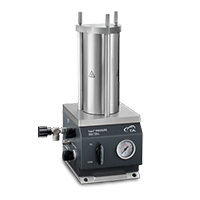
Oxidative Resistance Tests
Oxidative Induction Time (OIT) testing on polyethylene and polypropylene to determine level of residual antioxidants and level of oxidative stability
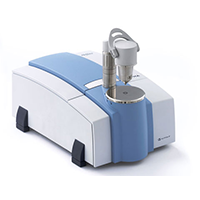
Analysis of Material & Structure
Analysis for material composition, structure, overall thickness & layer thickness is done using Fourier-Transform Infra-Red Spectroscopy (Transmission and ATR), Differential Scanning Calorimetry, digital microscopes, chemical tests, and more.
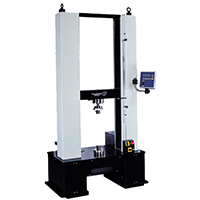
Tensile & Mechanical Tests
Mechanical properties are measured using computer-controlled Tensile test instrument, Dart Impact, and other equipment.
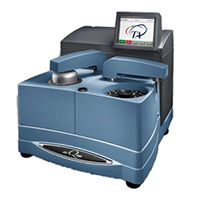
Other Physical Tests
Thermal Analysis, Oxidative Induction and other testing is done using Differential Scanning Calorimetry, Melt Flow Indexer, digital Microscopes, Slip Test equipment, ovens and more.
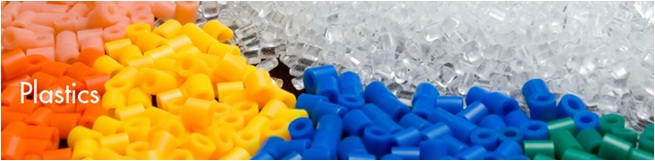
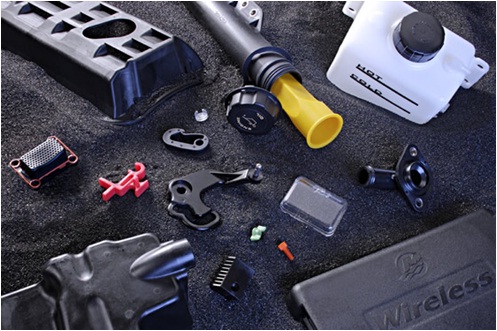
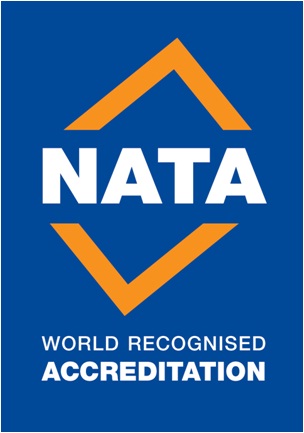
Polymer Testing provides a wide range of testing and analysis services the polymers and plastics industries. Our facilities for plastic product and process development utilise both pilot and full scale polymer processing equipment.
Polymer Testing is accredited by the National Association of Testing Authorities (NATA) and complies with the requirements of ISO/IEC 17025:2005 ‘General requirements for the competence of testing and calibration laboratories’.
Polymer Testing is run by highly qualified personnel who are experienced in industry and understand the need for work to be carried out to commercial timelines.
Polymer Testing Labs have extensive experience in polymer and plastics analysis and testing. Our polymer and plastic testing experts have investigated a wide range of polymeric materials, including:
- Thermoplastics
- Rubbers & Elastomers
- High-performance polymers
- Specialty polymers
- Geomembranes
- Composites
- Polyurethanes
- Adhesives & sealants
- Paints & coatings
- Films
- Thermosets
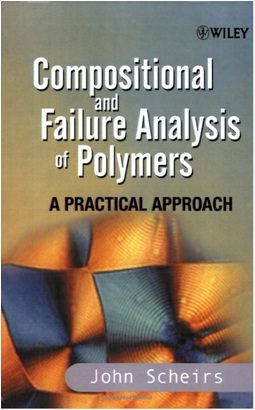
- Microscopy of Polymers
- Fourier-Transform Infrared Spectroscopic Analysis Methods for Polymers
- Thermal Analysis of Polymers
- Identification and Analysis of Polymers
- Analysis of Blends, Copolymers and Oligomers
- Identification and Analysis of Thermoset Elastomers
- Analysis of ‘Difficult’ or Intractable Polymer Samples
- Analysis of Additives in Polymers and Elastomers
- Analysis of Contaminants and Inclusions in Polymers
- Mechanical Failure Mechanisms of Polymers
- Chemical Attack of Polymers
- Oxidative Degradation of Polymers
- Failure of Fibre-Reinforced Composites.
- Problems Related to Additives in Polymers
- Weathering of Polymers
- Environmental Stress Cracking of Polymers.
- Residual Stresses and Weld Lines in Polymers
- Odour, Tainting and Outgassing Problems with Polymers
- Adhesion Problems with Polymers and Interfaces
- Voids, Blisters and Surface Defects
- Discoloration of Polymers
- Compositional analysis
- Raw material analysis (resins, additives)
- Comparative analysis
- Good vs. bad lot sample investigations
- Contaminant or impurity identification
- Deformulation (reverse engineering)
- Polymer failures
- Identification of suspect materials
- Off-color, off-odor problems
- Product failures
- Competitive product characterization
- Comparative analysis of “good” and “bad” samples
- Investigation of Product failure issues
- Identification of batch to batch variations
- Verification of marketing claims
- Patent infringement investigations
- Materials Analysis & Identification
- Mechanical Testing
- Deformulation
- Contaminant Identification
- Development of Plastic Product (Material Selection)
- Failure Analysis
- Ultraviolet Exposure
- Consulting
- Expert Witness/Litigation Support
Polymer Testing Labs have developed considerable expertise in identifying and characterizing unknown plastics and polymeric materials using analytical testing techniques and expert interpretation of results.
We perform polymer testing and identification using tools such as FTIR and NMR spectroscopy or DSC thermal analysis to determine the chemical family and functional groups through library matching and fundamental spectral interpretation. We can also identify the elemental composition of the inorganic components in an unknown polymer using a SEM equipped with EDAX.
- Density
- Tensile strength and modulus (standard and high speed tensile testing)
- Flexural strength and modulus
- Compressive strength
- Izod or Charpy impact
- Tensile impact
- Falling weight impact
FTIR – Fourier Transform Infrared Spectroscopy is the workhorse tool for identifying and characterising polymer materials and their additives. Polymer Testing uses a Bruker Diamond ATR FTIR. Spectra from unknown polymers can be readily compared with our extensive reference spectral library. The ATR method is a powerful technique in problem solving – particularly for the identification of inclusions or defects in moulded parts or plastic films. The carbonyl index using FTIR can determine the extent of surface oxidation of polymers.
DSC – Differential Scanning Calorimetryis a thermal analysis technique that measures heat flow to of from a polymer. By monitoring the heat flow as a function of temperature phase transitions such as crystalline melt temperature (Tm), crystallisation temperaturee (Tc) and glass transition temperatures (Tg) can be measured. Using the crystallisation temperature and %crystallinity the thermal history of a sample can be gained. The DSC technique can also be used to determine the thermal stability of polymers and their residual antioxidant/stabilizer levels by determination of the OIT (oxidation induction time)
TGA – Thermogravimetric Analysis (TGA) measures changes in the weight of a sample as a function of increasing temperature. TGA is used to determine polymer degradation temperatures, absorbed moisture content, residual solvent levels and the amount of inorganic (non-combustible) filler in polymer or composite samples. It can also assist in deformulation of complex polymer products such as rubber goods.
Elemental Analysis Microscopy – EAM is a powerful surface imagining technique which uses x-rays to determine the elemental composition of small samples.
- Identification of the polymer type to ensure that the correct or specified type of polymer has been used for the application or to identify unknown polymer materials
- To investigate the composition of copolymers and polymer blends using melting points and glass transition temperatures
- To identify and investigate polymer degradation mechanisms such as the oxidation of polyethylene or the hydrolysis of polyurethane
- To identify additives that have migrated to the surface of the polymer, such as phthalate plasticisers in PVC
![]() |
![]() |
![]() |
At relatively low levels of magnification it is possible to see manufacturing defects such as microcracks, inclusions, voids and flow lines, the dispersion and alignment of fillers and fibres. In addition it is possible to see the witness marks of physical contact or mechanical damage.
Scanning electron microscopy (SEM) can be used for characterisation of fracture surfaces or defective areas and identification of inorganic components or contaminants present.
Plastic deformulation involves using a range of analytical techniques and conventional extraction methods to identify and quantify the components of a complex polymer mixture including polymers, resins, fillers, stabilizers, plasticizers, lubricants, flame retardants, antioxidants etc.
Deformulation studies usually starts with grinding of the plastic to a fine mesh size followed by the following analytical techniques such as Fourier Transform Infrared Spectroscopy (FTIR), Differential Scanning Calorimetry (DSC), Gas Chromatography with Mass Spectral detection (GC/MS), Scanning Electron Microscopy/Energy Dispersive X-Ray Spectroscopy (SEM/EDS).
Additives in very low amounts may be determined using High Performance Liquid Chromatography (HPLC) and Gas Chromatography/ Mass Spectrometry (GC/MS). Gel Permeation Chromatography (GPC) can be used to determine the molecular weight and molecular weight distribution of the resin.
Polymer Testing Labs have worked on numerous contamination identification problems such as:
- Identification of foreign particles (e.g. inclusions, gels, etc.)
- Raw material quality issues (e.g. metal fragments)
- Off-color analysis (e.g. yellowing, pinking)
- Off-odor analyis (e.g. degradation)
- Manufacturing issues
- Problems with storage conditions
The presence of regrind or recyclate may be indicated by analysis of the metal catalyst residue from the polymerization catalyst in the resin. Each virgin polymer manufacturer uses a certain catalyst system, which may be different from the one used in the polymer regrind or recyclate. So the presence of two or more different residues might indicate regrind/recyclate in the sample.
Polymer Testing have the experience to provide you with a detailed materials input to guide your development process. Working alongside your design engineers Polymer Testing can offer their polymer expertise in a range of activities throughout the design process:
Feasibility Study
At the early stages of the design process we can conduct feasibility studies to assess the potential for the use of polymer materials within your design window by considering factors such as ease of processing, manufacturing routes and component durability .
Materials Selection
The first step in a successful product development process is the identification of the correct material for an application. With well over 15,000 polymer grades on the market this is no simple task. Polymer Testing have experience with working with all polymer materials and can make impartial recommendations for the correct polymer from any given application.
Mechanical Design Assessment
Polymer materials are viscoelastic in nature, their properties can also be highly dependent upon processing conditions and polymer flow. By application of thorough knowledge of the long term properties of individual polymer materialsExcelplas can assess component designs to ensure reliable long term durability.
Component Testing and Evaluation
Having produced prototype polymer components or first-off parts Polymer Testing can develop and conduct suitable accelerated test programmes to ensure the mechanical performance of polymer component parts are suitable for long term durable service. Working to standard test procedures or tailored designed programmes vital performance data can be generated within appropriate timescales and budgets.
Supported by our chemical analysis and mechanical testing laboratories Polymer Testing Labs are able to rapidly assess the cause of product failures and, importantly, recommend remedial action to minimise the risk of further failure.
Questions that are typically addressed include:
- Was the specified polymer fit for purpose?
- Is the failure an isolated incident or are a large number of products likely to be affected?
- Did the product performance specification adequately consider the known and reasonably foreseeable performance requirements?
- Did the polymer conform to the requirements of applicable standards or specifications?
- Was the specified material used?
- Was the design stress exceeded?
- Did contamination or interaction between materials result in a deterioration in performance?
- Is there any evidence of additive migration or diffusion?
- Are defects present arising from the manufacturing process?
- Did poor processing or installation result in a deterioration in properties?
- Is a product recall or a building closure necessary?
incorrect material selection – the use of an incorrect polymer for a specific application is a common cause of polymer failure. For instance, lack of understanding of the interaction of polymers with chemicals and environments commonly leads to premature failure;
inappropriate design – proper product design is fundamental to ensure plastic components will have long term durability. Poor design in combination with long-term loading, high speed loading, chemical environments, cyclic (fatigue) loads can cause brittle failure of the product within a short service life;
processing errors – incorrect processing of plastic materials can lead to failure via degradation and embrittlement process, material inhomogeneity, high residual stresses, inclusion of moulding defects or contaminants;
chemical & environmental factors– interactions betweens polymers with chemicals and environments can lead to degradation of cracking of polymers. For many polymers specific interactions with common household products can lead to rapid crazing, cracking, fracture and product failure.
Failure analysis of plastics and polymers can involve the fracture and failure of materials such as fibres, films and membranes, polymers, engineering plastics, composites, coatings and paints.
Polymer Testing expertise includes experience with design faults, moulding issues, stress, overload, degradation, unintentional service conditions, misuse and even sabotage.
Polymer Testing scientists have a deep knowledge of plastics and polymers raw material production processes, polymerization technology, moulding processes and end-user applications, which vary from simple packaging films through consumer goods to advanced aerospace materials.
Failure analysis work is carried out in support of customers’ own investigations, customer complaints or liability disputes, or as part of complex litigations cases.
Polymer Testing provides accelerated weathering testing to evaluate your materials or products by testing that simulates exposure to ultraviolet light.
Accelerated weathering simulates damaging effects of long term outdoor exposure of materials and coatings.
What can UV testing tell you about your product or material?
UV accelerated weathering or exposure testing evaluates your test sample for its reaction to photo-induced degradation. Photolysis is a chemical reaction that can affect brittleness, fading, cracking and other forms of deterioration as a result of exposure to ultraviolet radiation. One reason exterior coatings are so durable is because of the use of accelerated tests that simulate short wavelength UV and natural moisture.
Accelerated Weathering (QUV) is done to the following standards: ASTM G154, ASTM D4329, ASTM D4587, ASTM D7238, ISO 4892
![]() |
![]() |
![]() |
Our extensive experience allows us to recognize indicators of failure and track these leads to the root cause of failure.
Plastics failure can range from premature breakage (e.g. fracture) or discoloration. A sample of the “good” vs. “bad” product may be sent to our lab for comparative analysis. We also request a “reference sample” or “control sample” such as a historical samples or a competitor’s sample.
Examples of the polymer materials that have been the subject of failure investigations include:
- Packaging
- Laminates
- Geomembranes
- Composites
- Adhesives
- Coatings
Our laboratory includes a variety of instrumentation for failure analysis such as FTIR, DSC, optical microscopy, SEM/EDAX, TGA, TMA, GC/MS, NMR and GPC. Environmental chambers are also available for failure analysis and to test the effects of UV, heat and humidity on plastic products. To better understand the problem, we may recreate the failure conditions.
Our client’s PU laminating adhesive was not providing a full lamination bond with wrinkling and blistering occurring in heavy duty pet food sacks. Faced with production line shut-down and potential litigation, the customer called Polymer Testing. Our expert chemists determined the presence of silicone oils at the point of the disbonds using TOF-SIMS testing. The results showed significant levels of silicone in the films that were exhibiting delamination. The silicones were suspected to be from mold release sprays used in the blown film process.
Failure Investigations are led by Dr. John Scheirs. He has over 15 years experience with legal cases involving polymer failure and has acted as an expert witness in multiple court appearances in product failure and personal injury cases in Australia and NZ. During that time he has written numerous technical reports in litigation matters and insurance claims working as an expert witness.
With 25 years experience of Plastics Technology he has extensive knowledge of the performance of thermoplastic and thermoset materials and components with particular expert knowledge of failure analysis,processing faults, defect assessment and testing of both polymer materials and components with expertise in accelerated product life determination and accelerated ageing.
- Litigation support services include:
- Evaluation of cases
- Method development and testing
- Interpretation of technical data
- Critical review of data
- Literature searches
- Trial preparation
- Depositions and trial testimony
Our materials scientists have offered forensic testing and litigation support in insurance claims and litigation arising from polymer product failures such as flooding caused by burst plastic pipes or personal injury from plastic fracture.
Below is a list of our typical turnaround times for polymer and plastics for commonly requested polymer testing services:
- Melt Flow Index — 2 business days
- Density & Specific Gravity — 2 business days
- FTIR Spectral and Analysis — 2 business days
- Differential Scanning Calorimetry (DSC) — 3 business days
- Scanning Electron Microscopy (SEM) — 5 business days
- Elemental Analysis — 5 business days